- By Rapid Roofers
- Roofing
- 0 Comment
Are you looking for information on metal furring and its costs? Then you’ve come to the right place. This in-depth guide will go through all the essential things you need to understand about furring systems, as well as various considerations to keep in mind when picking out the right materials or system for your products.
We’ll also run you through the different types of metal furring available and provide a practical step-by-step guide on how to install them. We’ll also delve into the perks of using metal furring for your walls and ceilings and how to calculate the price.
For anyone navigating the particulars of screw placements, wool insulation challenges, or setting the perfect angle on a joist, this article is meant to give you an upper hand in both planning and execution.
Let’s delve in!
Understanding Metal Furring Systems
Did you ever wonder how structures achieve those perfectly smooth walls or slick ceiling designs?
Welcome to the world of metal furring, the unsung hero behind modern wall and ceiling finishes. Metal furring systems are instrumental when it comes to securing drywall, gypsum panels, and other wall materials such as masonry or metal structures.
Metal furring helps provide a completely level plane for materials such as tile or other finishes while also ensuring long-lasting durability. Unlike the more traditional wood framing, metal furring presents a robust, fire-resistant, and mold-free alternative. In this section, we’ll learn about metal furring‘s role in construction, dive into the materials that make up these systems, and weigh the benefits over wood framing, all the while keeping an eye on how these aspects influence current pricing trends.
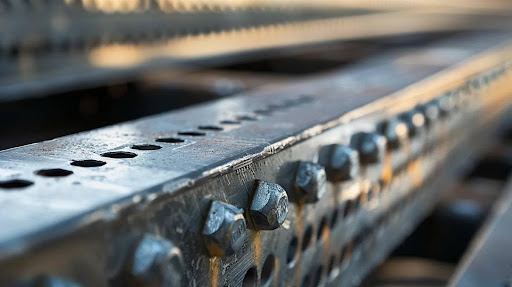
What Is Metal Furring and Its Purpose?
Metal furring is a construction technique where slim strips of metal, typically made out of steel, are used to create a framework. This structural framework is vital for attaching wall materials and helps in creating level surfaces for finishes. Used both in commercial and residential projects, including many in the Philippines, metal furring is used not only for mounting but also for enhancing certain features, such as soundproofing. The steel design ensures a level foundation, paramount in achieving those flawless walls and ceilings that stand out in modern architecture.
A traditional option to steel is wood. While wood has been a traditional go-to, steel wins hands down with its resistance to fire and immunity to mold. In projects where durability is non-negotiable, metal furring steps up. Not the least in tropical climates like the Philippines, where rust-resistant galvanized steel is a game-changer in battling humidity and seasonal weather. The choice between wood and steel furring greatly depends on the specific needs of the structure and it’s climate. In any case, steel invariably takes the price when it comes to longevity and maintenance.
Common Applications of Metal Furring in Construction
In the world of construction, metal furring systems are most commonly used in creating the skeleton for drywall in both residential and commercial buildings. Their practical role also includes attachment points for insulation materials, which are essential in modern and energy-efficient building designs.
Furring channels are perfect for accommodating wiring and plumbing work, allowing the contractors to neatly tuck away the necessary installations behind ceiling and wall coverings for a clean look.
Moreover, the rather specialized use of tin, wire, and nails in the installation of metal furring strips exemplifies their versatility. Whether you’re securing external cladding systems or providing a sturdy backing for intricate tile work in a remodelling, the precision offered by these systems is indispensable. This method simplifies the preparation for a variety of finishes, ensuring that any subsequent building efforts are supported by a reliable and level framework.
Materials and Components Used in Metal Furring
The core components of metal furring rely heavily on the manufacturing of precision-engineered sheet metal, which is specifically designed to be utilized in construction. This production process results in durable tracks and studs, which form the backbone of metal furring systems. The studs act as vertical supports, while the tracks, often featuring a U-shaped flange, secure the system at both the top and bottom, providing a framework to which drywall and other wall materials can be properly attached.
During installations in plumbing and electrical systems, metal furring components tend to be very valuable by enabling seamless integration. For example, the pre-punched holes in the metal strips allow builders to easily weave plumbing and wiring through the framework. This compatibility simplifies the coordination of different trades on the construction site, allowing for a smooth blend of structural and functional elements within the walls without compromising the integrity of the finished surface.
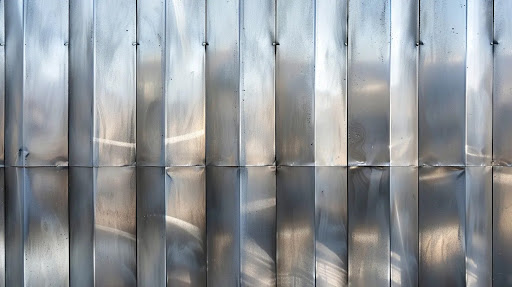
Differences Between Metal Furring and Wood Framing
The main notable difference between metal furring and wood framing comes down to material durability. Metal strips, unlike wood lath, are resiliant to shifts in moisture and temperature, making them much less likely to warp or rot. Metal’s inherent strength compared to wood also allows for wider spacing between framing units, which also reduces material needs and can result in cost savings, especially when considering the current pricing for wood and steel.
From an installation standpoint, the lightweight nature of metal furring further simplifies the job for contractors. This efficiency in framing effectively complements modern methods where timing is critical. Moreover, metal systems are uniquely conducive to integrating high-quality mineral wool insulation and cement board products, helping to provide superior fire protection and acoustic dampening. These factors, along with the ease of running lighting conduits through the pre-punched service holes of the metal framework, showcase the functional advantages that tends to make metal furring the preferred choice in various construction scenarios.
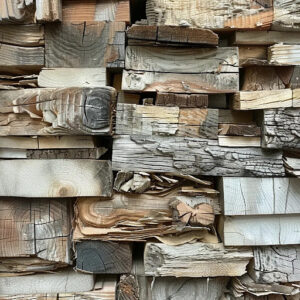
Different Types of Metal Furring
Diving into the specifics of metal furring, we’ll uncover a variety of types that cater to different construction needs. From the robust hat-shaped furring channels ideal for plaster or concrete attachments to the versatile Z-channels used in roof assemblies, each has its distinct applications. With an emphasis on soundproofing, resilient channels come into play, featuring compatibility with mineral wool for enhanced acoustics.
Steel and aluminum furring systems will be juxtaposed, examining their strengths and suitability for different projects. This section guides readers in selecting the right metal furring type with practical insights into current pricing trends and material benefits, all while keeping language straightforward and jargon-free.
Hat-Shaped Furring Channels Explained
Hat-shaped furring channels are a popular choice among contractors due to their unique configuration that offers superior rigidity and ease of attachment. Named for their resemblance to an upside-down “hat” profile, these channels are adept at providing a stable anchor for plasterboard or ceilings to masonry, concrete, or steel. The design optimizes material usage and can contribute to both cost efficiency and structural integrity in various building projects.
In the current market, the demand for efficient and high-performance construction materials has elevated the role of hat-shaped furring channels. These components are often selected to align with sustainability goals and energy codes, especially when considering their use in thermal bridging reduction. The industry trends show a keen interest in these durable channels as they blend cost-effectiveness with functionality, making them a smart investment in today’s construction environment.
Z-Channels and Their Uses
Z-channels are a versatile product when it comes to metal furring, and are frequently used in roof assembly to manage rainwater drainage and insulation. These channels provide a sturdy layer between the roof deck and the final exterior surface, which helps with both water management and thermal insulation.
The design of Z-channels allows for secure installation and effective anchoring of roofing materials, which makes them a vital part of modern construction. Price-conscious builders often appreciate Z-channels for their balance of cost and performance, ensuring projects stay within budget without compromising on protection against the elements.
Resilient Channels for Soundproofing
Resilient channels are used for noise-blocking, and are designed to effectively mute the transmission of sound waves through walls and ceilings. These thin metal channels work by decoupling the drywall from the structural studs,interrupts the path of sound and brings a welcome piece of silence to living spaces. In bustling urban homes or other noise-sensitive environments such as recording studios, these channels are a safe bet.
Another factor that adds to the popularity of resilient channels is their affordability especially when considering the current pricing trends in the construction market. As cost-effectiveness becomes increasingly important to builders and homeowners, these channels provide an economical solution without sacrificing quality. Resilient channels are a smart investment that reaps long-term benefits for anyone looking to create a tranquil environment against the backdrop of a noisy world.
Comparing Steel and Aluminum Furring Systems
When considering the right furring system for a construction project, builders often weigh the pros and cons of steel versus aluminum. Steel furring systems are immensely popular due to their strength and cost-effectiveness, making them a go-to choice for projects requiring heavy-duty support. Aluminum, on the other hand, brings the advantage of being lighter and resistant to corrosion, often chosen for projects that demand a lighter touch and areas with high humidity or coastal environments. Current pricing trends show that while aluminum furring systems can be more expensive upfront, they offer longevity that may provide better value over time, especially in scenarios where environmental considerations play a major role. Contractors and builders seeking to balance budget constraints with performance needs carefully consider these factors, ensuring their choice aligns with both the short-term financial realities and long-term durability expectations of their projects.
Selecting the Right Metal Furring Type for Your Project
When selecting the right metal furring type for a project, understanding the specific needs of the structure is crucial. For instance, in areas that are prone to moisture or coastal environments, aluminum furring systems are preferable to steel due to their superior resistance to corrosion. On the other hand, if the project demands a budget-friendly option with an additional focus on strength, steel furring systems might be the ideal choice.
The current price of materials can also influence the choice of metal furring. Builders might need to consider the fluctuating costs of steel and aluminum and assess which option aligns with their budget without compromising on quality. It’s important to strike a balance between financial constraints and structural necessities to ensure the longevity and integrity of the construction project.
Step-by-Step Guide to Installing Metal Furring
Step-by-Step Guide to Installing Metal Furring
Installing metal furring can transform a space, providing the perfect backdrop for sleek walls and ceilings. Before diving in, one must prepare the workspace and gather the necessary tools. The process begins with meticulous measuring and planning of the layout, ensuring each furring channel is accurately placed. Secure installation is crucial, as is following safety protocols to avoid mishaps. This guide also highlights common pitfalls to sidestep during the installation process. The following sections detail each step, making the intimidating task of furring approachable and error-free.
Preparing the Workspace and Required Tools
Preparing the Workspace and Required Tools
Before the first furring strip is even considered, clear the area to ensure a safe working environment free from potential hazards. It’s also a time saver to assemble all necessary tools beforehand, such as a laser level, drill, fasteners, snips, and screws specifically designed for metal work. A well-organized space allows for a smoother installation process and avoids delays that can be costly, especially when current pricing trends in the construction industry are factored in.
It’s vital to familiarize oneself with the specific type of metal furring system being installed, as different systems may require unique tools and approaches. For example, installing resilient channels for soundproofing may necessitate specialized fasteners to maintain their acoustic properties. A properly prepared workspace, complemented with the right tools, not only streamlines the installation process but also ensures that the furring is installed correctly, securing the value of one’s investment in the long run.
Securing Furring Channels to Surfaces
Securing Furring Channels to Surfaces
Getting the furring channels attached securely is at the heart of the installation process. Use suitable fasteners and anchors for the specific type of underlying surface; for masonry, one might need concrete screws, whereas for metal structures, self-tapping metal screws will do the trick. It’s all about choosing the right hardware to ensure the furring channels hold firm, directly impacting the longevity and safety of the finished walls or ceilings.
During installation, spacing between the channels should adhere to the manufacturer’s specifications to prevent sagging of the material that will attach to it. Properly spaced and secured metal furring channels provide a solid base necessary for achieving smooth wall finishes and are a key factor in evaluating the cost-effectiveness of the project, given current material prices and labor considerations.
Safety Tips During Installation
Safety Tips During Installation
When tackling the installation of metal furring, safety must take center stage to prevent any construction mishaps. Enthusiastic DIYers and experienced contractors alike should always don protective gear such as gloves, safety glasses, and hard hats when working. Clear communication among team members is also crucial, especially when installing at heights or handling heavy materials, to avoid accidents that could derail the project and add unforeseen costs.
Handling metal furring requires a keen eye for detail and an unwavering commitment to safety guidelines. One should ensure electrical tools are in good working condition and that the workspace is free of clutter to minimize the risk of trips and falls. With metal edges being sharp, careful handling can prevent cuts and injuries. These thoughtful practices not only protect those on-site but also help keep the project aligned with current pricing trends by reducing delays due to injuries.
Common Mistakes to Avoid
Common Mistakes to Avoid
One common error in metal furring installation is neglecting the importance of checking for levelness throughout the process. Furring channels that are not perfectly horizontal can lead to an uneven finish that not only looks unprofessional but might also affect the integrity of the wall or ceiling. Considering current pricing trends, this mistake could add unnecessary costs due to the need for rectifying the work, highlighting the importance of getting it right the first time.
Another pitfall to steer clear of is overlooking the manufacturer’s instructions regarding the spacing of furring channels. Incorrect spacing can cause structural weakness, making the surfaces susceptible to damage and increasing the possibility of costly repairs down the line. Constructors must remain attentive to the specifications, ensuring their work provides a sturdy, even base for materials to come, thus maintaining control over material expenses and labor outlays in a fluctuating market.
Benefits of Using Metal Furring in Construction
Benefits of Using Metal Furring in Construction
Metal furring is more than just a support system for finishes; it brings a multitude of benefits to construction projects. Enhancing structural integrity, metal furring allows for improved thermal and acoustic insulation, which is vital in today’s energy-conscious climate. Its durability and longevity stand out, promising performance that lasts. With cost-effectiveness over time and a positive environmental impact through sustainability, this section delves into how metal furring could be the smart choice for builders and homeowners alike.
Enhancing Structural Integrity
Metal furring boosts structural integrity by providing a robust framework that supports wall and ceiling materials. This method not only ensures that drywall and other finishes are perfectly level and secure but also enhances overall building stability. With steel‘s remarkable tenacity, walls and ceilings maintain their form without sagging, even over the long haul, which makes metal furring a clever choice in climates and regions with great variations in temperature and humidity.
For builders and homeowners concerned about longevity and resilience, metal furring stands as a cost-effective ally in the construction process. Current pricing trends suggest that investing in metal furring can lead to savings by minimizing the need for future repairs and maintenance. A fortified structure backed by metal furring channels equates to one less worry, ensuring that homes and buildings can stand up to life’s knocks with unwavering grace.
Improving Thermal and Acoustic Insulation
Metal furring champions the cause of greater energy efficiency by creating a tighter building envelope for enhanced thermal insulation. By providing a separate space for insulation materials, heat transfer is minimized, contributing to a comfortable indoor climate and potentially lowering heating and cooling costs. This feature is especially relevant for property owners monitoring current pricing trends, seeking to balance upfront installation costs with long-term energy savings.
Along with thermal regulation, metal furring systems also contribute significantly to soundproofing efforts. Utilizing metal framing allows for the incorporation of acoustic dampening materials like mineral wool between the channels, reducing noise transmission and creating quieter living spaces. In an era where urban noise pollution is a growing concern, the value of a peaceful home environment is immeasurable, making metal furring an attractive addition for residents and contractors alike.
Durability and Longevity of Metal Furring
Metal furring systems stand out for their resilience. Crafted from materials like galvanized steel, they resist wear and tear that wood framing can fall prey to, such as warping, rot, or damage from pests. This makes metal furring a solid backbone for construction projects, promising longevity and sturdiness that can last for decades, unaffected by internal or external stresses.
The practicality of these systems shines when one factors in sustainability and current pricing trends. Reduced need for repairs and replacements means metal furring is not just a tough choice but also a smart one financially. Builders and owners can rest easy knowing that, despite upfront costs, the return on investment over the life of a structure is often substantially greater when compared to less durable alternatives.
Cost-Effectiveness Over Time
Metal furring might seem like a significant investment upfront, but the cost-effective nature becomes evident over time. The durability of materials like galvanized steel means maintenance and replacement costs are lower compared to traditional wood framing, which requires more frequent updates due to issues like warping or termite damage. For those keeping a watchful eye on construction expenses, the longevity of metal furring provides a return on investment that continues to benefit the homeowner and builder over the years.
Another aspect of the cost-effectiveness of metal furring systems is their role in energy conservation. By creating an optimized space for insulation, metal furring contributes to better thermal regulation of buildings, leading to reduced energy bills. Over time, the savings in heating and cooling costs can be substantial, offering a financial upside for property owners who are aware of the importance of energy efficiency in today’s building practices.
Environmental Impact and Sustainability
Metal furring has a reduced environmental footprint due to its sustainable nature, which aligns with the evolving priorities of today’s construction industry. The use of recyclable materials like steel not only minimizes the impact on forests by avoiding the need for timber but also allows for a lower waste profile through the lifecycle of a building. Builders are now leveraging metal furring to meet green building standards and attract homeowners interested in environmentally friendly construction practices.
Furthermore, metal furring contributes to energy efficiency, a critical aspect of sustainable building design. By facilitating tight insulation installation, metal systems help reduce energy consumption for heating and cooling, thus decreasing the carbon emissions associated with excessive energy use. This factor is a strong selling point in the current market, where buyers and constructors alike are conscious of both the ecological and economical benefits of energy-smart building features.
Factors Affecting Metal Furring Pricing
Factors Affecting Metal Furring Pricing
Within the realm of construction, understanding the pricing of metal furring systems is complex and influenced by a myriad of factors. Material costs and market fluctuations play an intricate role, often swayed by shifts in supply chains and the availability of materials. Regional differences further complicate pricing, with geographic variables affecting costs significantly. Large-scale projects and bulk purchases may offer economies of scale, while the chosen brand and quality of metal furring can cause prices to swing. In the following sections, these pivotal considerations will be broken down, offering practical insights into their impact on metal furring pricing.
Material Costs and Market Fluctuations
Material Costs and Market Fluctuations
The cost of metal furring systems is tightly linked to the rollercoaster ride of market fluctuations and raw material prices. For instance, steel prices can soar or dive based on global demand, trade policies, and production levels, directly impacting the budget for construction projects. Builders and buyers must stay alert to these economic winds, as they can vastly alter the cost calculations for both residential and commercial builds.
Local market variations also play a significant role in the pricing of metal furring materials. A region’s proximity to manufacturing facilities or ports can either drive up costs due to shipping or lower them thanks to easy material access. Contractors need to keenly assess these geographical factors and adjust their estimates accordingly, ensuring clients receive a clear picture of the financial implications for their specific location.
Conclusion
Conclusion
Metal furring presents a robust solution for achieving perfect wall and ceiling finishes, offering enhanced durability, improved insulation, and cost savings over time. Opting for metal over traditional wood framing accommodates modern construction needs, resisting environmental factors like moisture and providing fire resistance. With material costs and market conditions influencing prices, builders must navigate these with strategic timing and supplier relationships to maintain project budgets. Understanding the various types of metal furring, their applications, and current pricing trends equips professionals with the knowledge to make informed, quality-driven choices in an ever-evolving industry.